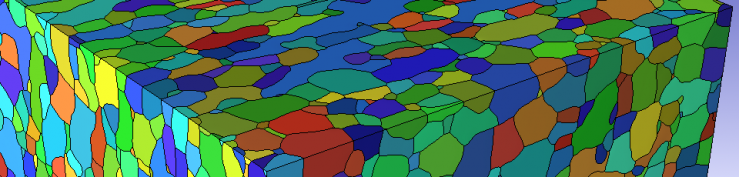
Model Courtesy UCSB Materials Department
Meshing of Microstructures
The Challenge
To predict the behavior of complex material processes at the continuum scale, a good understanding of the underlying microstructure is required. Finite element simulations can provide that insight. However, a finite element analysis depends on the availability of a quality 3D mesh of the microstructure, while the microstructure data often exists only in the form of a 3D voxel data set. The 3D voxel data sets are typically generated by 3D imaging processes (e.g CT scan), reconstruction from data such as Electron Backscatter Diffraction (EBSD) measurements, or software that creates a synthetic 3D microstructure. This leaves the analyst with the difficult task to create a proper finite element mesh from a 3D voxel data set.
The Solution: Tools to Integrate Microstructure Analysis into a Finite Element Workflow
With Simmetrix' advanced modeling and meshing functionality, microstructures are easily converted to input for finite element solvers.
Capabilities include:
- Eliminate data processing artifacts in the microstructure data.
- Create fully valid geometric models from microstructure data.
- Support the efficient application of analysis attributes.
- Generate high quality finite element meshes.
- Export the analysis information to an input file for a finite element solver.
- Retain association of results all the way back to microstructure grains
Benefits:
- Solve material process problems that were out of reach to date
- Save cost by prototyping with software instead of expensive testing
- Perform non-destructive analysis of parts deployed in the field
- Increase ROI through faster development to market time
Above is a standard microstructure dataset from DREAM.3D. The left shows the model after smoothing has been applied, the right shows the mesh, generated using curvature-based refinement as well as a background mesh size.