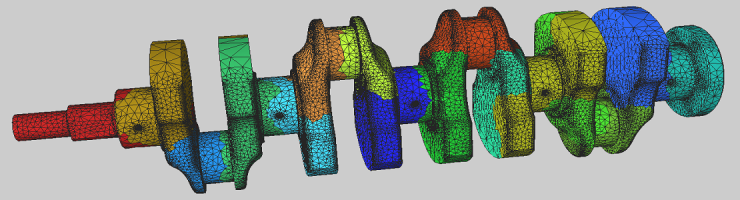
Parallel Meshing
Overview
Simmetrix' parallel meshing technologies provide for the generation and adaptation of surface and volume meshes in a distributed parallel environment. These capablities allow your large scale adaptive simulations to run entirely on the same parallel computer using functional interfaces between analysis and meshing, removing the need for expensive serialization or disk I/O.
Parallel meshing is fully automatic: all domain decomposition and load balancing is automatic and internal. As with serial meshing, the parallel partitioned mesh is always associative with the true CAD model and conforms to geometric boundaries.
Multithreaded meshing is also separately available to fully employ all cores of your machine and speed up mesh generation and adaptation procedures.
Capabilities:
- Automatic partitioning and load balancing during mesh generation and adaptation.
- Full conformance to the real CAD geometry.
- Parallel support is available for a large majority of corresponding serial capabilities.
- Meshes in the billions of elements have been generated and adapted on thousands of processors.
- Support for any MPI implementation (MPICH, OpenMPI, MS-MPI, your own).
- Rich set of partitioned mesh related data structures and API functions to run large scale adaptive simulations without bottlenecks.
Parallel Mesh Generation
Mesh generated in parallel on 16 processors for a given wing geometry. Colors denote mesh parts on different processors. Surface mesh of wing and cut view showing 3D boundary layer mesh are shown. This mesh has 2M total elements out of which 1M are in the boundary layer. A much finer mesh was generated for the actual analysis; a coarser one is shown so the connectivity is readily visible.