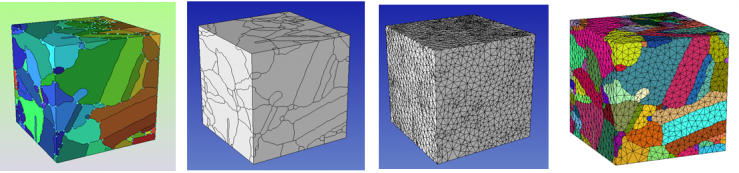
Case Study - Johns Hopkins U.
Implementation of Simmetrix in a Framework for Microstructure-based Modeling of Metallic Materials
Dr. Somnath Ghosh
Michael G. Callas Chair Professor
Department of Civil Engineering
Departments of Mechanical Engineering and Materials Science & Engineering
Johns Hopkins University
The mechanical properties of metallic materials are determined by the underlying microstructures, e.g. grain distribution, precipitates, micro-twins and etc. Such microstructures are often heterogeneous and affect deformation mechanisms and damage characteristics locally. Conventional analysis use phenomenological models which do not adequately account for the effect of microstructure and often failed to predict the material behaviors, e.g., they are incapable of capturing the strength dependence on precipitates or resistance to fatigue.
Recent years have seen a paradigm shift towards the use of material microstructure-based detailed mechanistic models for predicting. Experimental serial sectioning techniques, e.g. using focused ion beam (FIB) and electron backscatter diffraction (EBSD) mapping provide large three dimensional datasets with detailed morphological and crystallographic information. The inclusion of these geometric complexities in mechanical models requires the development of tools to handle actual experimental datasets and tools to mesh them for eventual finite element (FE) simulation. Some of the key data processing steps are primarily accomplished through the usage of Simmetrix.
In this report, research accomplishments using Simmetrix on three important alloys, namely nickel-based superalloy, magnesium alloy AZ31, and titanium alloy Ti-6242 are summarized.
Simmetrix for Modeling Ni-based Superalloy Applications
For Ni-based superalloys, two different spatial scales control the overall mechanical behavior of the material. The first scale is at the micron level where simulations can be performed on polycrystalline aggregates consisting of variously oriented grains and annealing twin structures. The second scale, on the order of hundreds of nanometers, is at a subgranular level where a two phase precipitate-matrix system is observed. The precipitates have three dimensional shape and spacing characteristics that affect the single crystal behavior of the superalloy[1] (Keshavarz and Ghosh, 2013).Polycrystalline Microstructures
Rene88-DT is a Ni-based superalloy developed for jet engine turbine applications, which has a polycrystalline microstructure interspersed with twin boundaries resulting from the annealing process. When attempting to retain the geometric complexities of the annealing twins for the subsequent FE analysis, many issues arise in treating and smoothing the voxelized dataset and preparing it for a tetrahedral mesh (Fig. 1).
The twins are typically at a finer length scale than the parent grain, and the experimental resolution may not be high enough to avoid breaks and hooks in the microstructure. To deal with such a structure, Simmetrix provides tools to filter and smooth the dataset and to allow the majority of the key features to be passed to the FE mesh. An example of a data treatment procedure is shown in Fig. 2.
Figure 1 (at right )René-88 DT polycrystalline EBSD reconstruction displaying (I) fine scale features, (II) “hooked” grain boundaries, and (III) isolated defects within grains (dataset from W. Lenthe, T. Pollock)
Figure 2. (below) Filtering and smoothing process to transform an EBSD reconstruction to a FE mesh[2]
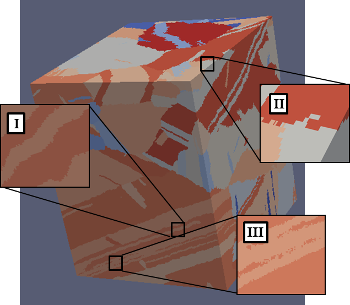
The primary steps in constructing a virtual microstructure include volume thresholding, erosion, dilation, edge refinement, boundary smoothing, vertex repositioning, and curvature refined meshing. The attributes of the original microstructure are then mapped onto the resultant elements of the mesh and simulations are performed. A multi-scale Ni-based superalloy model is used as the constitutive response for the material and includes mechanical effects from the subgrain morphology (Fig. 3).
Figure 3. Simulation results (right) showing local equivalent plastic strain field for a polycrystalline specimen model (left) generated using Simmetrix. Constant strain rate test condition is applied.